‘To be able to take what is basically a rock and carve and shape it into something more refined is immensely satisfying” says Eric Byrne, a second generation master stonemason based in the grounds of Russborough House in Wicklow. His workshop is in a fine 18th-century courtyard on the estate where he has painstakingly restored a stable block since moving in last year and where, fittingly, craftsmen of another era would have carved and polished its sturdy granite pillars by hand in a pre-power-tool age.
“Granite is a very tough material to cut even with today’s diamond saws and they must have done these pillars with a hammer and chisel and then smoothed them out,” he says, slowly stroking a surface in admiration. He works with Connemara marble, Kilkenny marble and limestone and Dublin/ Wicklow granite and is a storehouse of information on the wonder of their origins 400-750 million years ago.
In the showroom, his latest collection of cheeseboards, serving platters and cake dishes are made from these unique green and black Irish stones combined with pure white Macedonian Sivec, which he explains was used by the Romans until Michelangelo made Carrara fashionable. The white slab is cleaved by an arrow of green marble while another is bisected by lustrous black. The cheeseboard’s Connemara herringbone pattern, like a piece of marquetry in marble is particularly striking bringing out the serpentine richness and wild natural patterns of the stone.
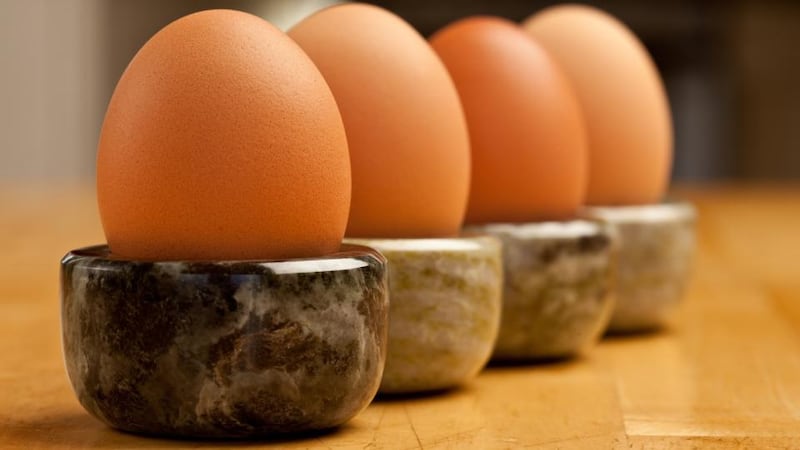
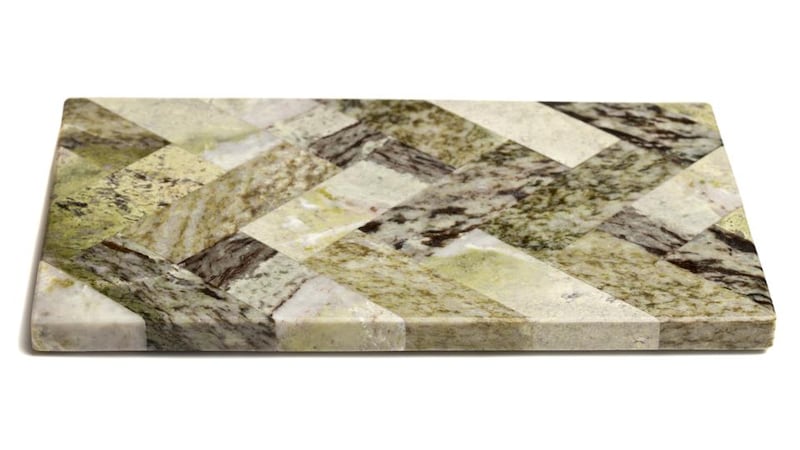
“What I love about Connemara marble is the variation of colour – though it can be a nightmare when you are trying to match pieces as a set. If you cut one foot square of it into strips, there is such variation that you could swear that they came from another quarry. It is a fascinating stone to work with. There is nothing boring about it. Abroad it is called Irish Green and you will find it in rock-star kitchens,” he smiles.
At his father’s side
From Lucan and the son of a stonemason, he grew up at his father’s side watching and working “as soon as I could hold a shovel”, he says. His father Christy’s speciality was Terrazzo flooring including parts of Dublin Airport in the 1960s and later monumental work and fireplaces. “I always enjoyed working with him – you would be handed a hammer and chisel or even an angle grinder and told, get on with it. I remember going with him to cemeteries or fitting fireplaces and finding it all so interesting. I started full-time work at 16.”
In the 1990s, however, when the first phase of cheaper imports of pre-made fireplaces began and work became sparse, he moved to a marble granite supplier in Coolock – “hard, long days”, he recalls before starting his own business making kitchen counters and worktops. With the crash in 2008 he realised that he needed a change of direction into smaller, more exportable products to survive.
“I reasoned that working with Irish stone which was more expensive would be one up on stone imported from China or India using different designs and different materials which these countries don’t have.”
Today, the shiny floor in the studio of speckled patchworked South African marble and steps of Sardinian stone – waste counter tops – are testimonies to his earlier, larger scale work. With the “massive support” of quarry owners such as Kevin Joyce in Connemara and Jim Harding in Kilkenny, he started afresh in December 2010 setting up Hennessy & Byrne (Hennessy being his wife’s maiden name) making smaller pieces. Since then, the range has developed exponentially and now includes everything from whiskey stones and Christmas decorations to napkin rings, salt and pepper sets and larger table-top items.
Formidable
The transition took time. “With big pieces machinery and tools work around the stone, but when you are working with smaller items, you have to move the stone around the machines. It takes a bit of ingenuity to figure out how to make the product.” The machinery looks formidable – rolling bench saws for small and accurate cutting and bench drills that are water fed to keep the diamond cutter cool, wash out silt and ensure clean cutting without dust. He has skilfully adapted water troughs once used for washing out animal waste to recycle water with a waste pump and hose system. Elsewhere there’s a router for cutting intricate shapes in stone and any amount of polishing equipment including an ingeniously modified belt sander originally used for buffing hurleys.
Polishing is key. “Any stone that can be polished to a high shine is commercially classified as marble,” he explains. “Cutting the stone is the easy part – most of the time goes into polishing to get the finish and shine right with a series of polishing grits or pads.” To explain, he demonstrates how a compressed-air drill with a rubber bushing is used for chamfering or bevelling the edges of a marble napkin ring. Outside the workshop rough slabs of marble, limestone and granite await his hand.
“Stone is rough in its natural form compared to the end finish which is gleaming, shiny, smooth and polished. The first thing visitors do is touch the marble and realise that something as hard and cold as stone can give that soft smooth feeling.” Now a regular exhibitor at Showcase, he launches his new Marmar range next month in Create at Brown Thomas.
As to the future, a third generation of Byrnes is already showing a fascination with stone so another stonemason may be in the making.
hennessyandbyrne.com