Every day along the river Liffey in Co Kildare, more than 20 million litres of water briefly disappear.
Sucked out at a treatment plant, its journey brings it through complex networks of pipes, purifying filtration systems, storage tanks and treatment pools before it all eventually spills back into the river not far from where it initially left it.
It is no secret that the materials in Intel’s highly sophisticated microprocessors – those that power PCs and cloud servers – are cleansed in pools of super-clean Liffey water, a river baptism of sorts.
Hundreds of millions of gallons loop their way around the company’s Leixlip campus each month through arteries of brown pipes that form an elaborate, dizzying circulation network, a life support system without which their semiconductors could not survive. It is a confluence of nature and technology, the former nourishing the latter in early life.
READ MORE
But Intel does something remarkable with the Liffey water, transforming it from the murky brown fluid familiar to most Dubliners into ultrapure water (UPW), something so pristine as to be unconsumable.
“If you compare sewage to drinking water, it’s about 10 times purer in terms of the solid inside it. If you take drinking water to ultrapure water, it’s a million times purer,” says John Flood, the plant’s senior facilities engineer who is responsible for this river alchemy.
“You can’t drink it, basically it would strip the ions from your body. If you go for a run and take an isotonic drink, it’s the exact opposite of ultrapure water; you put all these ions into the water to recover yourself. But ultrapure water is doing the opposite.”
In large enough quantities, it would probably kill you.
In September, Intel – one of Ireland’s most successful foreign direct investment stories, employing about 5,000 people in a campus that takes on the form of a mini-city – opened its latest advanced chipmaking facility.
Fab 34 produces wafers with Intel 4 technology, using extreme ultraviolet (EUV) lithography. The process transfers patterns to a silicon wafer, creating the blueprints for integrated circuits. It is worlds away from a humble beginning in which chip boards were assembled on the site of a disused car dealership in Palmerstown.
Sitting about 3km northwest of the Liffey, the sprawling factory has formed a unique reliance on its water supply. Without borrowing its relatively small daily allowance of river water, it would be impossible to manufacture its computer chips, so minute that their silicon requires the most delicate of rinsing between each manufacturing step.
“We make the smallest things ever made by mankind in pretty much some of the biggest factories that ever existed,” says Michael Cullen, Intel’s senior environmental engineer.
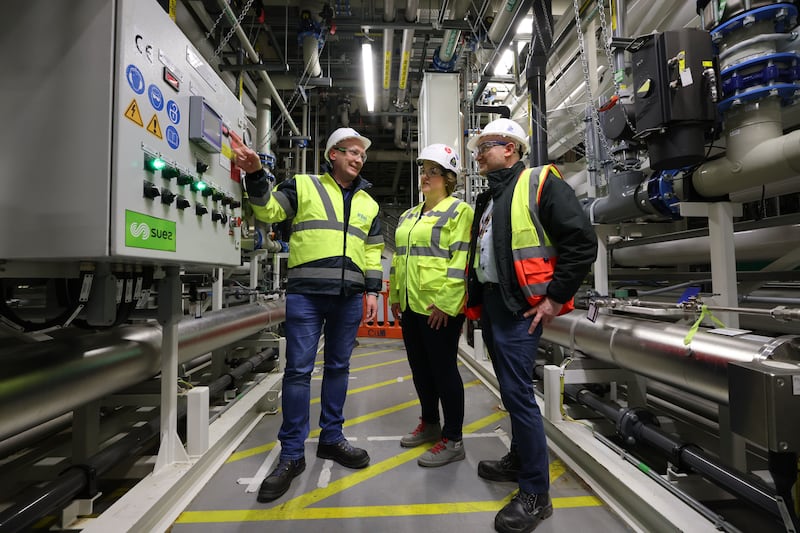
Cleanliness is next to godliness at Intel. Its manufacturing clean rooms use air filtration systems to keep the space particle free – in “class one” areas, there are no more than 1.25 micron particles per cubic foot of air.
Intel workers suit up to enter these spaces, giving the manufacturing areas the appearance of a virus lab. In reality, of course, the suits are to protect the chips, not the workers.
Water quality is crucial because the materials they make are extremely sophisticated. The Intel 4 transistor is seven nanometres in size, the equivalent of seven seconds of human fingernail growth.
Given a dust particle might measure between 100 and 200 nanometres, such a lump would smother the surface of a transistor, potentially causing an electric short or creating a hole in the chip.
“Particles are defects, so the water is flushing that away. But if you flush that away with dirty water you’re just adding more [particles] on to it,” says Flood.
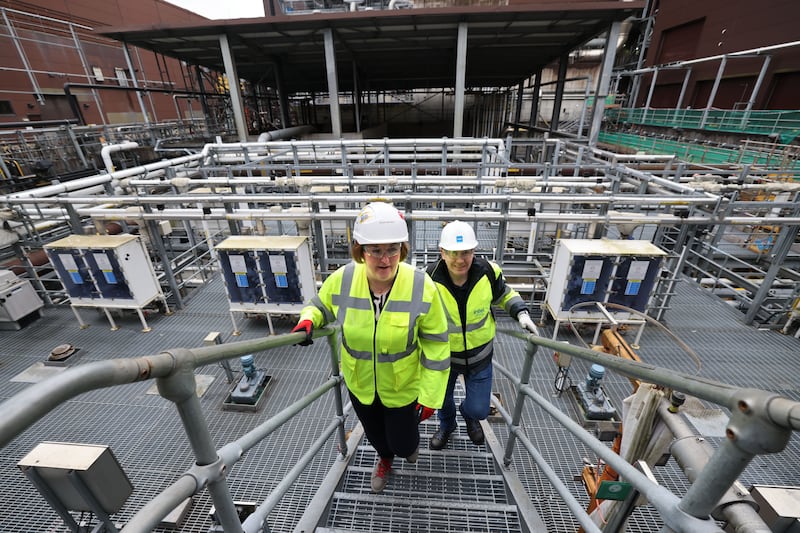
The water that flows the length of the Liffey has many uses but none so delicate as what takes place at Intel. The process undertaken to achieve it is meticulous, any potential cause of contamination stamped out at design.
The plant takes in about 660 million litres of water per month, or about enough to fill 264 Olympic-sized swimming pools. Once it has flushed through the facility, carrying out its various duties, 580 million litres, or 232 swimming pools worth of water, is returned to its natural source.
Once the potable quality supply enters the facility, a rough filtration and cleaning removes solids. That is followed by a process of reverse osmosis, and a fine cleaning that strips out the ions before a “polish stage” removes gas. Storage is critical – exposure to the natural atmosphere would immediately recontaminate the water and so it is kept safely beneath a layer of nitrogen.
During the UPW processing stage, the factory had once been losing about 25 per cent of water that could not be rendered suitable for use. In recent years, however, a new nanofiltration system has been used to clean this excess so that it can be pumped into other parts of the facility for other tasks. Consequently, only about 6 per cent of the water initially taken from the river is now deemed “useless” and moved straight to pre-release treatment.
About 88 per cent of all the water used by Intel is ultimately returned to the Liffey and most of the remaining 12 per cent is lost to evaporation. The company’s aim is to bring that to 100 per cent or more – with the gap made up by off-site projects such as a recently launched bogland rewetting project in Co Wicklow that will replenish water storage in the Liffey.
A brief stroll around the Intel campus can prove disorientating, its walkways curling in and around massive pipes and air ducts, steel tanks and endless brown monolithic walls. At any given point, somewhere among the vast steel inner workings of the plant, Liffey water is running towards its objective or on its way back to the river course.
“All of the waste is segregated into specific waste drains. So we have a huge number of waste drains that run essentially from the factory floor ... all the way down to the back of the site,” says Sinead Garrigan, facilities engineer in wastewater, of the used liquid.
“And it’s all segregated into the associated collection tanks. If you take a particular type of waste drain, it’s segregated into a particular tank.”
Then it is either treated on-site or a small amount of it, essentially diluted chemicals, is taken off-site by tanker trucks.
Once brought to a certain standard, the bulk of the water is returned to the Leixlip treatment plant where, processed alongside other effluent, it returns to the river, eventually making its way through the city and out to sea.