She sings. She sparkles. And she’s made by women paid just 1c for each doll that shimmers off shop shelves.
This Christmas, tens of thousands of children the world over will excitedly tear the wrapping paper off an Ariel doll – Disney’s Little Mermaid – secure in the knowledge that it was made for them by Santa’s happy elves at the North Pole.
The reality would come as a cruel surprise. For elves, read Chinese factory workers. For the North Pole, read the city of Heyuan. And for happy, read miserable – from illegally long working hours and exhaustion to wages too low to support a family.
An investigation published on Thursday by rights groups Solidar Suisse and China Labor Watch found evidence of excessive and illegal overtime, basic pay rates as low as 96c an hour, no holiday or sick pay and high levels of exhaustion among the largely female workforce making toys for Disney, Mattel's Fisher Price brand and other international toy companies.
Daily overtime varied between two and five hours, and with weekends included, overtime would sometimes hit 175 hours a month – nearly five times the legal limit of 36 hours
Staff at the Wah Tung factory in the city of Heyuan said that they worked 175 hours of overtime in a month, with only one day off over that period – both breaches of Chinese labour law and toy industry codes of conduct.
The basic hourly wage on the line is 7.5 Chinese yuan (96c) – legal, but so low that workers say they feel obliged to work overtime. The investigation also highlighted a significant gender imbalance, with men outnumbering women nine to one in management roles but women making up 80 per cent of the workforce.
Heyuan is a city of roughly 3 million people in Guangdong province, south-east China. It is home to Wah Tung (Heyuan) Toy Manufacturing Ltd, where about 2,000 workers produce a range of mainly plastic toys and electronics. This is where Disney makes the Princess Sing & Sparkle Ariel doll that sells for €34.99. Many online stores have sold out of stock and are awaiting a fresh delivery a few days before Christmas. At the peak of production, in late summer, as many as 2,400 of the dolls were rolling off the Wah Tung production line each day.
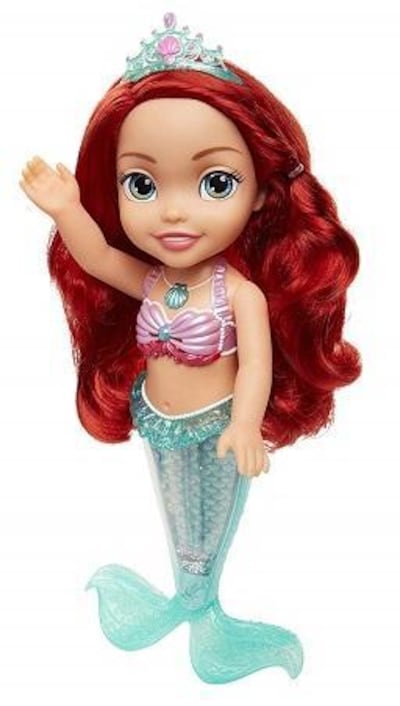
The doll comes with a mane of deep-red hair and a glittery tail that acts like a snow globe. In the last quarter it helped Disney’s consumer-products division to an operating income of almost €300 million on revenue of almost €1 billion.
But the investigation found that, when costs were broken down, each of the women on the production line was receiving barely more than 1c for every doll produced. (This figure represents the total monthly wages of the 36 women on the production line, working an average of 26 days a month, divided by the total number of dolls produced each month.)
The investigator joined the Sing & Sparkle assembly line for a month during the summer. From her own experience and interviews with fellow workers, she found daily overtime varied between two and five hours and that, with weekends included, overtime would sometimes hit 175 hours a month – nearly five times the legal limit of 36 hours.
In low season, workers earned about 2,000 Chinese yuan a month (€256); during peak season, they generally took home about 3,000 yuan (€384). A survey last year put the average Chinese monthly salary at 7,665 yuan (€980).
Workers were expected to arrive 10 minutes before the start of their shifts; many reported feeling excessively tired because of the long hours. Photographs from the production lines show workers asleep or resting during breaks.
In her diary, the investigator noted: “At 5pm, the worker behind me said she felt so tired that her back was sore. She wanted to sleep so badly but couldn’t, since our shift wasn’t over yet. She wondered why was time going by so slowly. I said that I also felt time was going by very slowly. When you’re constantly doing the same thing over and over again, you start to feel dizzy and your vision becomes blurry.”
She also noted that most of her colleagues were women over the age of 45 who were drawn to the work because they were “poorly educated, well-behaved, obedient, and care more about children and family”. Factories like them because “they are less likely to make trouble and easier to manage” than men, she wrote.
“There were a lot of female workers at the toy factory and some of them were older. So, when they worked, they needed to wear reading glasses. They worked very carefully and quickly, but some of the time, the line leader would say they worked too slowly or would yell at them. Whenever the female workers were being yelled at, they would never say a word in return and would silently continue working on the task at hand.”
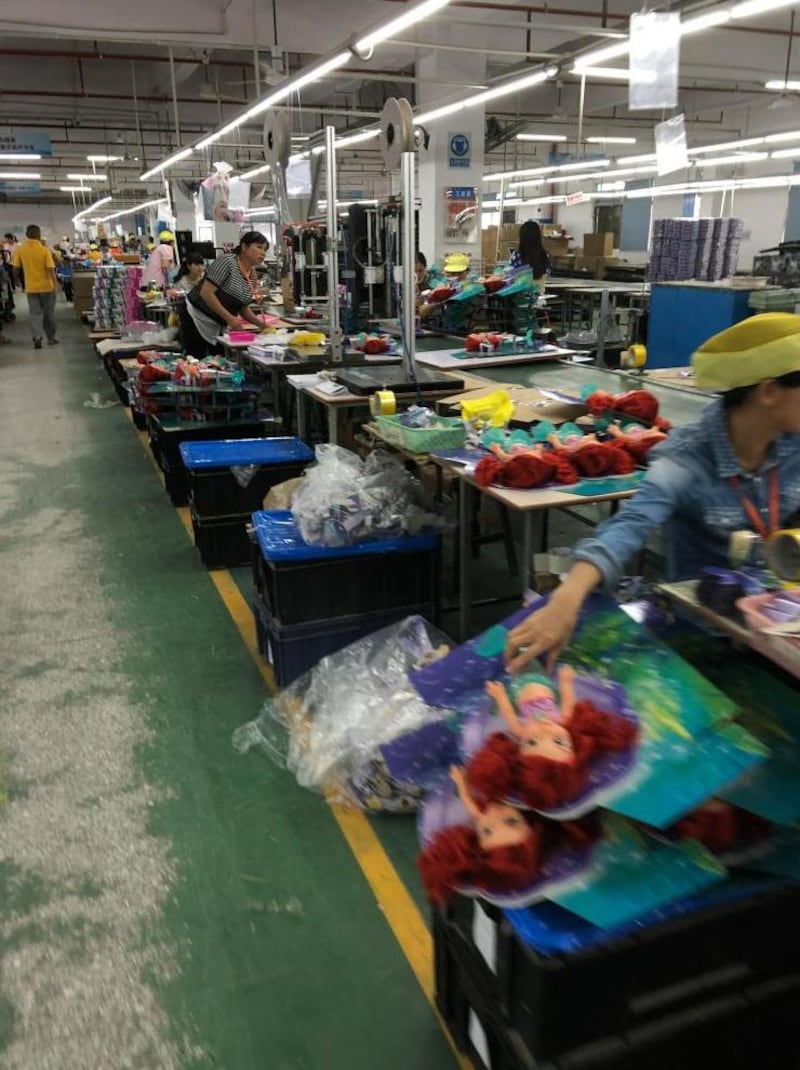
Simone Wasmann, from Solidar Suisse, urged toy companies to share some of their profits with workers. "Children love Disney's toys but we want their parents to understand that there's no Christmas magic going on here: those toys were made with cheap labour by women working illegally long hours for pennies. For them, it is just day after day of misery. They don't work in those factories long into the night because they want to: they do that because it is the only way they can make enough money to live."
She said Disney could afford to pay higher prices to ensure wage increases. “It’s time the company gave something back to the people who make their merchandise by raising their wages, cutting their hours and making the factories obey the law [on overtime]. A few pennies on the price of a doll or a few pennies less in the company’s pockets would enable workers to earn a living wage.”
Many of the biggest toy makers, including Disney and Mattel, are members of the International Council of Toy Industries, which sets out expected industry standards as part of an ethical toy programme intended, the body says, to improve working conditions in toy factories.
The Wah Tung factory is certified by the ICTI. Speaking on the factory’s behalf, the ICTI spokesman Mark Robertson said: “The allegations highlighted from the CLW report contravene ethical toy programme’s own requirements on working hours, wages, holiday pay and annual leave. We will work directly with factories to address any issues identified. We take the issues raised by China Labor Watch very seriously and have launched our own investigation. We will quickly and effectively address any issues identified which are in breach of our standards.”
Robertson said that the ICTI had achieved substantive progress in raising ethical conditions at the organisation’s certified factories in China and elsewhere. “Wages have increased, factory environments are safer and working hours are reducing; hours worked at toy factories in China are lower than those in the apparel and electronic sectors.”
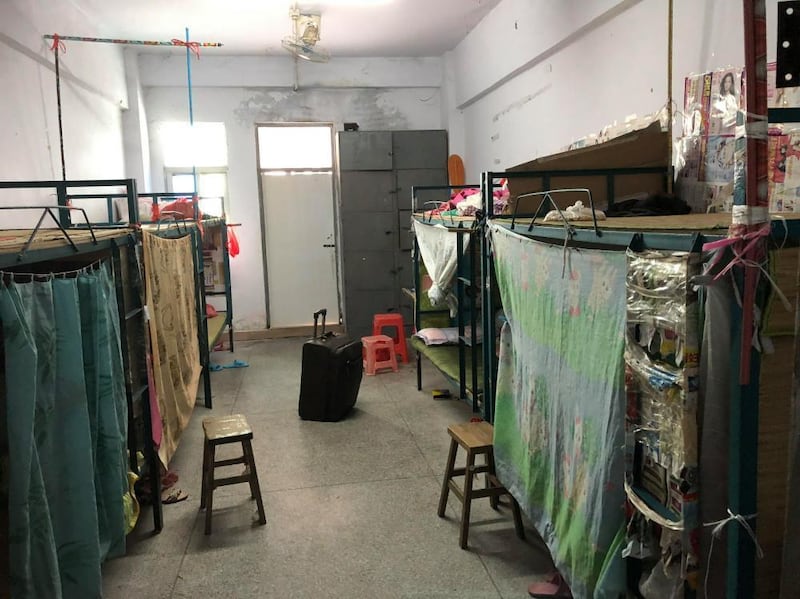
A spokesman for Disney said the brand was a member of the ethical toy programme’s committed brands plus programme, which it used alongside others “as part of our responsible sourcing approach”. He referred to a statement from the ICTI in which the council said it welcomed “any robust investigation which increases our understanding of working conditions at toy factories”.
Mattel said it had no current production in the factories mentioned in the CLW report. “Mattel is committed to ensuring every single person making our toys and products is treated fairly, with respect, and is able to work in a safe and healthy environment. Our labour standards, environmental, health and safety programmes and oversight processes reflect this commitment, and we stand behind our record of ethical labour practices and environmental stewardship.”
Three other factories producing for a large number of international brands feature in the full report. – Guardian