A wood-burning stove is simmering in Tom Cussen’s workshop as he works on a 1930s Gibson tenor banjo. “It was in rag order when it got here,” says Cussen, whose business, Clareen Banjos, has been making and restoring banjos for more than 40 years.
The workshop is dusty but organised. One table is stacked with part-finished banjo necks, still awaiting final shaping by hand and decorating with mother of pearl, after being hewn from “exotic” woods.
Cussen’s workshop is behind his home just outside Clarinbridge, Co Galway. The business showroom is next to the workshop, and his voice, along with that of his son Fintan, resonates off the decades-old vintage and brand new instruments hanging all around them as he recalls his early days in banjo playing and instrument making.
‘I made my first banjo from local wood in 1985. All the parts were brought in at that time except the wood... The company as it is now started as a hobby’
“The business started primarily because of my involvement in music. Why the banjo? The folk boom of the 1960s and then I got in a band,” says Cussen. “I effectively was an accordion player before I started playing the banjo.”
READ MORE
One broken accordion helped sway Cussen towards his brother’s banjo before he left Galway for London in 1968. There, he picked up his first banjo for just £10. The band he joined, and is still part of, was the trad group Shaskeen.
“I would credit London with my immersion in music, and that was my passion and it still is... I’m celebrating more than 50 years with the one band, and we’re still going and the banjo has been part of that for 50 years.
“The banjo was gathering interest because of the folk boom and I was interested because it was like having your first car – you were always maintaining it.”
Cussen, who once worked as an electrical engineer and is still making and restoring banjos today at the age of 76, returned to Galway in 1971 and gradually began buying and restoring vintage banjos from 1974 onwards.
“I made my first banjo from a kit in 1979 which was subsequently stolen [from its next owner at a French campsite],” says Tom. “I suppose I made my first banjo from local wood in 1985. All the parts were brought in at that time except the wood... The company as it is now started as a hobby.”
“When I started out, I effectively made three models,” says Cussen. “I had the Special – which is the bread-and-butter banjo – and that’s the one we sell the most of. Then we made the Pearl and the Oyster, and the reason for those is [that] Clarinbridge is oyster country.”
The name of the company itself came from the village, Clareen being derived from Droichead an Chláirín.
The showroom was once the main workshed for Clareen but after a visit to a luthiers’ guild convention in Nashville in 2000, Tom decided it was time to take things up a gear and a new, larger workshop was built to the back of his home. (A luthier is a craftsman who builds or repairs string instruments that have a neck and a sound box.)
“We were working in isolation because we had no tradition or no format for making these things... it was all by trial and error to a large degree.”
Since the late 1980s, Clareen has made several thousand banjos and shipped its products, primarily tenor banjos along with the occasional five-string banjo and mandolin, all over the world to places as far away as Brazil, Korea and Japan. Between 40 and 45 per cent of Clareen’s output is exported, mostly to the US.
“I’m not saying I was the first person ever to make a banjo in Ireland,” says Tom. “But certainly we were the first people to manufacture banjos in any kind of quantity, and we’re still learning.”
Fintan Cussen came back from Australia in 2003 and joined the business, initially to help handle the paperwork.
‘One of the great satisfactions in what we do is when somebody sits down to play a banjo that you made specifically for them and their eyes light up’
“I can’t take any credit for what came before [I joined],” says Fintan. “All I have tried to do is maintain [our] reputation and build on it to a point where we’re as busy as we’ve ever been in the past 20 years... There’s a huge amount of people starting, people playing. It’s one of the more popular instruments. The banjo is in a very good place at the moment.”
Clareen employs four people in total, and is confronting the modern challenges that face businesses large and small.
“The issues we’re facing at the moment are the same as businesses thousands of times our size,” says Fintan.
“Shipping, the cost of everything... the cost of materials have gone through the roof. If I wanted to ship a banjo to the United States three years ago, it was €70. It’s costing €180-€190 today. Brass has doubled in price... the wood we use is exotic wood, there’s a scarcity to it but the cost of that is probably going to have doubled when we reorder it.”
Despite the difficulties faced by Clareen and other small Irish businesses, there is confidence about the future, especially given the talent in younger players now, who Fintan believes are better than their 1960s and 1970s counterparts due to the wealth of information and teachers available. The growing popularity of the instrument can be credited to classic players such as Barney McKenna, who helped secure the banjo’s place in Irish traditional music, alongside contemporary players such as Gerry O’Connor and We Banjo 3′s Enda Scahill, a winner of the 2022 Steve Martin Banjo Prize.
Clareen sources all of its materials sustainably. Its wood is Forest Stewardship Council (FSC) stamped and includes rosewood, several types of maple, and Irish sycamore.
“We only deal with companies that have all the [FSC] certificates... the mother of pearl [used for inlaid designs on the fretboards of instruments] is reconstituted from crushed shells.”
Fintan picks up a banjo from behind where he’s sitting in the showroom. Its neck came from a sycamore that came down in the midlands during a storm about eight years ago. A man came to use their workshop for a project of his own and he offered Clareen the fallen tree.
“It came down in the back of a truck, it was a massive tree,” Fintan says. “We had to bring it to a sawmill to get it cut into manageable planks, we had to leave it dry for nearly five years and we just started using it this year.”
Alongside their strivings toward sustainability, Clareen is keen to work with other Irish businesses to secure materials and parts for their instruments.
“We try to use small businesses around the country. For our nickel plating, for example, we use a small business in Dublin. There’s other guys that do smaller bits and pieces,” says Fintan.
“It’s all down to quantity,” says Tom.
Fintan adds that they don’t make smaller parts such as the tension hooks and tuning pegs: “If you were making every part of every instrument, you’d probably make 10 a year. Now it’s at a stage where there’s certain volumes that just couldn’t physically make them and you couldn’t make them in Ireland. They’d be impossible to make at the quantity we need them.”
“The hooks,” Tom says, “I went to a local tool shop here in Galway. I showed [the owner] the hook and asked, ‘Could you make these?’ And he said, ‘Shouldn’t be a problem, how many do you want?’ ”
Tom was looking for between 2,000 and 3,000 units. The tool shop also had a metal-machining business based in Clare and initially said they only dealt in units of hundreds of thousands.
The company’s foreman, however, said it would be possible to produce the parts in smaller quantities and the hooks are still made in Ennis, Co Clare, to this day. Tom and Fintan are keen to continue to explore new techniques and ideas that can be implemented into the production process.
Number 12, the twelfth instrument ever made by Tom, is still hanging in the showroom and still in perfectly playable condition
“In instrument-making in Ireland, things have improved massively in the last 30 years, primarily because of the internet and availability of information,” says Tom. “Like any hobby, you want to improve on it, you go to the ends of the earth to get your Ps and Qs right. Skills can be attained and improved on and evolve.”
The skills in the business have evidently evolved over the decades to help grow their product selection from the three models Tom once offered to a catalogue of banjos to suit different budgets and tastes.
“We get a good few customised requests. Certain things we would guide people away from because while it might look good when it’s brand new, it may not age well. Something like gold plating at the moment is so expensive, so we try to guide people away from that... but when it comes to designs on the neck and stuff like that, anything is possible,” says Fintan.
Tom credits Fintan with introducing new materials at processes into the building stages of the instruments, such as Teflon coating instead of expensive and dirty nickel plating, and thoughts have turned to how other materials such as carbon fibre can be practically incorporated into future designs.
Clareen’s top-of-the-line banjo, The Setanta, costs roughly €4,500. While this may seem a lot, Tom says: “The price is only ever justified if someone is willing to pay that kind of money, because they have to see the value in it.”
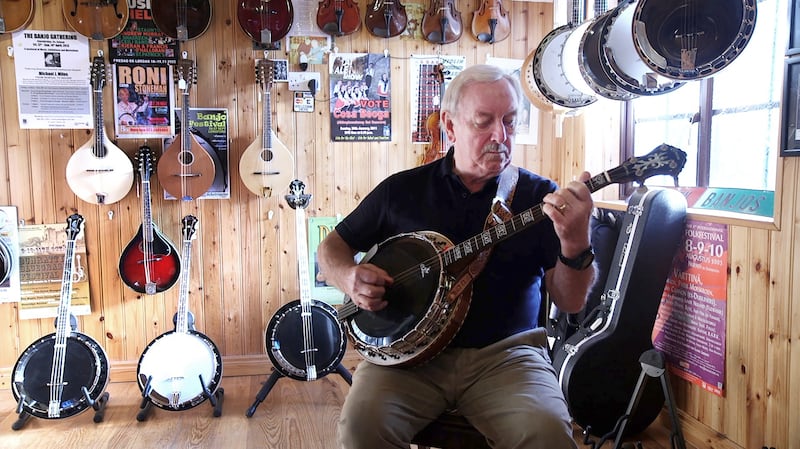
“One of the great satisfactions in what we do is when somebody sits down to play a banjo that you made specifically for them and their eyes light up – that moment is the most satisfying moment in the whole thing, because they’re surprised and shocked that you got it better than they were actually hoping for. You could make thousands of banjos and if nobody likes them, there’s no point. They have to like what we make... They only buy it because they want it, and the value is justified in them wanting it.”
Tom and Fintan are adamant that their product is built to last and several of the decades-old banjos hanging in the showroom are testament to this.
“There’s 100 years in those [banjos] with reasonable care,” says Tom.
“They’re built to last,” says Fintan. “There’s longevity in them, they will last a lifetime.”
The pair look back to the wall behind them and Fintan points out that Number 12, the 12th instrument ever made by Tom, is still hanging in the showroom and still in perfectly playable condition, looking every bit as good as the day it first left Clarinbridge. A Special model from 1988, it was bought back from the person it was originally sold to.
The Special is still part of their product range and helps tie the modern business back to its earliest days when Tom was still working solo and part-time.
“It’s the same banjo, we’ve just got better at making it,” says Fintan. “We have definitely got better at making; our finish is as good today as it has ever been.”